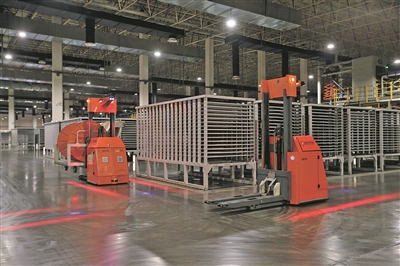
2月10日,在贵州轮胎旗下载重子午胎分公司生产工厂,AGV自动导向搬运车正按照指令搬运货物。 贵阳日报融媒体记者 杨才江 摄
贵阳日报融媒体记者 魏宏 周小游 庭静
当地时间1月20日19:00,在达沃斯世界经济论坛年会举办的第五届全球“灯塔工厂”颁奖典礼上,贵州轮胎登上领奖台,捧起了这个代表当今全球制造业领域智能制造和数字化最高水平的“灯塔工厂”奖杯。
这是中国轮胎制造业和贵州首个“灯塔工厂”。
代表贵州轮胎登台领奖的是贵州轮胎信息技术部部长韩洪川。在全球瞩目的颁奖仪式上,他用五分钟慷慨激昂的英语演讲,向世界发出了“贵阳智造”的好声音——
“我们相信,通过团队协作,能够实现目标、创造奇迹。”韩洪川坚定地说:“借助先进技术,我们开启了创新之路,实施了40多项第四次工业革命技术解决方案,如人工智能辅助设计、先进数据分析、灵活绿色生产,以确保轮胎质量并提高生产效率。”
“灯塔工厂”是由世界经济论坛和麦肯锡咨询公司共同遴选的“数字化制造”和“全球化4.0”的示范者,被誉为“世界上最先进的工厂”。
这束贵阳“智”造之光如何点亮“全球灯塔”?2月10日下午,贵阳日报“新春走基层”采访团队来到位于修文县的贵州轮胎股份有限公司生产基地进行探访。
从“人海模式”到“智能工厂”
贵州轮胎旗下载重子午胎分公司生产工厂的主要产品为卡车、客车轮胎,是5G全链接智能生产工厂,也是世界经济论坛先进制造与供应链中心重点评估的关键对象。
走进载重子午胎工厂时,记者最直观的感受便是生产车间先进智能化技术的创新应用。占地258亩的生产线,并没有想象中的灯火通明、机器轰鸣、工人忙碌……与之形成鲜明对比的是一切安静有序,无人操作的40余台AGV自动导向搬运车穿梭在整洁的车间中,若干机械手臂和胎圈机器人精准地操作着各道工序,从物料存储、发料、取料到产品制造、包装、出货,数据自动采集、设备互联互通,生产全流程自动化。
在三角胶热贴自动生产线上,工人赵祖发通过智慧屏对若干机器人发出指令。“过去,一线工作是‘人海模式’。现在,动动鼠标、点点屏幕就能比以前干得更好更快。”得益于智能化设备的运用,赵祖发的工作看上去并不费力。
“仅胎圈全自动一体化成型系统这一项解决方案的运用,就让我们的工人减少50%、运转时间下降90%、生产效率提高60%、一次性合格率提高15个百分点。”韩洪川说。
世界经济论坛先进制造与供应链中心总负责人基瓦·奥古德表示:“纵观我们的‘全球灯塔’网络,数字技术正在掀起一场生产生态系统革命。从人工智能驱动的控制塔到零代码工作流程,‘灯塔工厂’完美展示了可持续创新,为成千上万企业树立了榜样,有望推动整个生态系统的转型和变革。”
世界经济论坛指出,贵州轮胎此前面临的挑战在于满足客户多样化的定制化订单(占比60%以上)需求,这要求实行严格的设计、验证和可靠性标准。
为加速产品设计,确保持续、稳定的产出,贵州轮胎实施了40多项第四次工业革命技术解决方案,提高生产制造的敏捷性和生产率,最终让产品缺陷减少57%、劳动生产率提高68%、库存水平降低34%。
聚焦高效、智能、绿色等关键词,贵州轮胎收获了“灯塔工厂”这个全球亮眼的标签。
从“敢为人先”到“长期主义”
“我们一直在前进!”这是采访团队在贵州轮胎听到最多的一句话。
到底是什么技术推动着贵州轮胎一直前进,让“全球灯塔”在中国西南的一个小县城点亮?我们得到的答案是:在数字化转型战略下,通过一代代贵州轮胎人孜孜不倦的转型探索和接续奋斗。
“并不是某一项技术的创新或突破成就了灯塔荣耀,而是由若干智能化制造解决方案综合评价而成。”贵州轮胎股份有限公司副总经理蒋大坤说,“这些先进制造的解决方案不是一蹴而就的,而是长期积累下来的。”
从制造走向“智”造,贵州轮胎这条路走了20多年——
“早在2000年,为促进各业务管理部门协同、实现信息数据共享、提高管理效率、降低各环节资金占用、减少呆坏账损失,公司投入近千万元开发上线了ERP系统。”蒋大坤回忆道,正是因为那时的敢闯敢试,才在贵州轮胎漫长的转型之路上埋下了全域数字化的种子。
2000年至2017年,信息化系统实施分领域建设,夯实基础,完成ERP、PLM、CRM等经营管理平台系统建设,MES系统逐步在各分公司试点实施。
2018年,开展企业数字化转型顶层设计,对信息化现状进行调研与分析,提出未来数字化转型应用架构顶层设计方案,明晰未来信息系统实施部署策略、项目实施规划以及投资预算分配。
2019年至2021年,开始数字化建设,以精益管理体系(GTPS)为基础,深化以MES系统为核心的数字化建设,实现工厂数字化覆盖,逐步开启营销、研发、采购等各专业领域的数字化建设。
2022年至2024年,全面引入物联网技术和人工智能技术,广泛接入5G网络、实现车间无人化、少人化管理。通过大数据平台为企业管理层提供决策分析。逐步实现供应链高效协同,实现销售、采购、生产统一化管理。
“这些年,我们通过AI赋能全流程研发设计、机器视觉精准检测、大语言模型驱动设备运维、AI赋能需求预测与产销协同、绿色智造双线并行等智能制造的五大创新实践,在效率、质量、成本提升和绿色转型等方面实现了从量变到质变的飞跃。”蒋大坤说。
从“本土深耕”到“海外拓展”
大年初四一大早,贵州轮胎总经理助理、载重子午胎分公司总经理王立杰按下了载重子午胎分公司生产线的启动键。“我们要全力推进复工复产,奋力冲刺一季度‘开门红’。”王立杰说。
获评“灯塔工厂”后,王立杰接受媒体采访的次数明显增多,面对记者的提问,他说得最多的还是那句话:“我们一直在前进。”
“获评‘灯塔工厂’并不是结束,而是对我们前期努力成果的肯定。接下来,我们将加速以人工智能为代表的新一代信息技术和先进制造技术深度融合,培育形成一批未来制造模式,持续推动变革创新。”王立杰说,“举例而言,我们的硫化机设备综合效率(OEE)从原来的74%提升到现在的83%。别小看这9个百分点的提升,对我们而言,一两个百分点都是生产效率的大提升,目前世界最先进的OEE水平也就是85%,我们已经接近这一指标。”
技术创新、科技创新成为推动轮胎行业发展的核心动力,智能化、绿色化成为轮胎行业的新趋势。
站在新一轮科技革命和产业变革的历史性交汇点,贵州轮胎深刻认识到第四次工业革命技术将为公司带来前所未有的发展机遇。
“灯塔”为我们照亮了什么?
回答记者提问时,王立杰表示:“我下个月就要去越南,前往贵州轮胎的越南前江基地,建一个比‘灯塔工厂’更先进的智能化工厂。”
作为贵州轮胎建设的首个海外工厂,越南前江基地是贵州轮胎融入“一带一路”建设、积极提升国际竞争力的重要战略部署。王立杰介绍,当前的“灯塔工厂”主要生产的是卡车、客车轮胎,历经炼胶、半部件、成型、硫化、检验等环节,全是信息化、智能化的高品质打造过程,越南前江基地即将建设600万套半钢子午线轮胎项目。
“这个项目我们筹备半年了。这次去,主要是负责厂房建设、工厂建设、设备安装、产品试制等工作。”王立杰说。
为实现公司的“国际化、智能化、绿色化、高端化”战略,贵州轮胎将持续研发具有更高性能和附加值的轮胎产品,推进生产流程的高度智能化和自动化,创新技术实现节能减排和资源循环利用,加强与科技企业、高校的技术和人才合作,以提质、降本、增效、安全、环保为价值导向,推动第四次工业革命技术在全业务领域不断深入融合与应用。
(《贵阳“智”造之光点亮“全球灯塔”》由贵阳日报为您提供,转载请注明来源,未经书面授权许可,不得转载或镜像。)